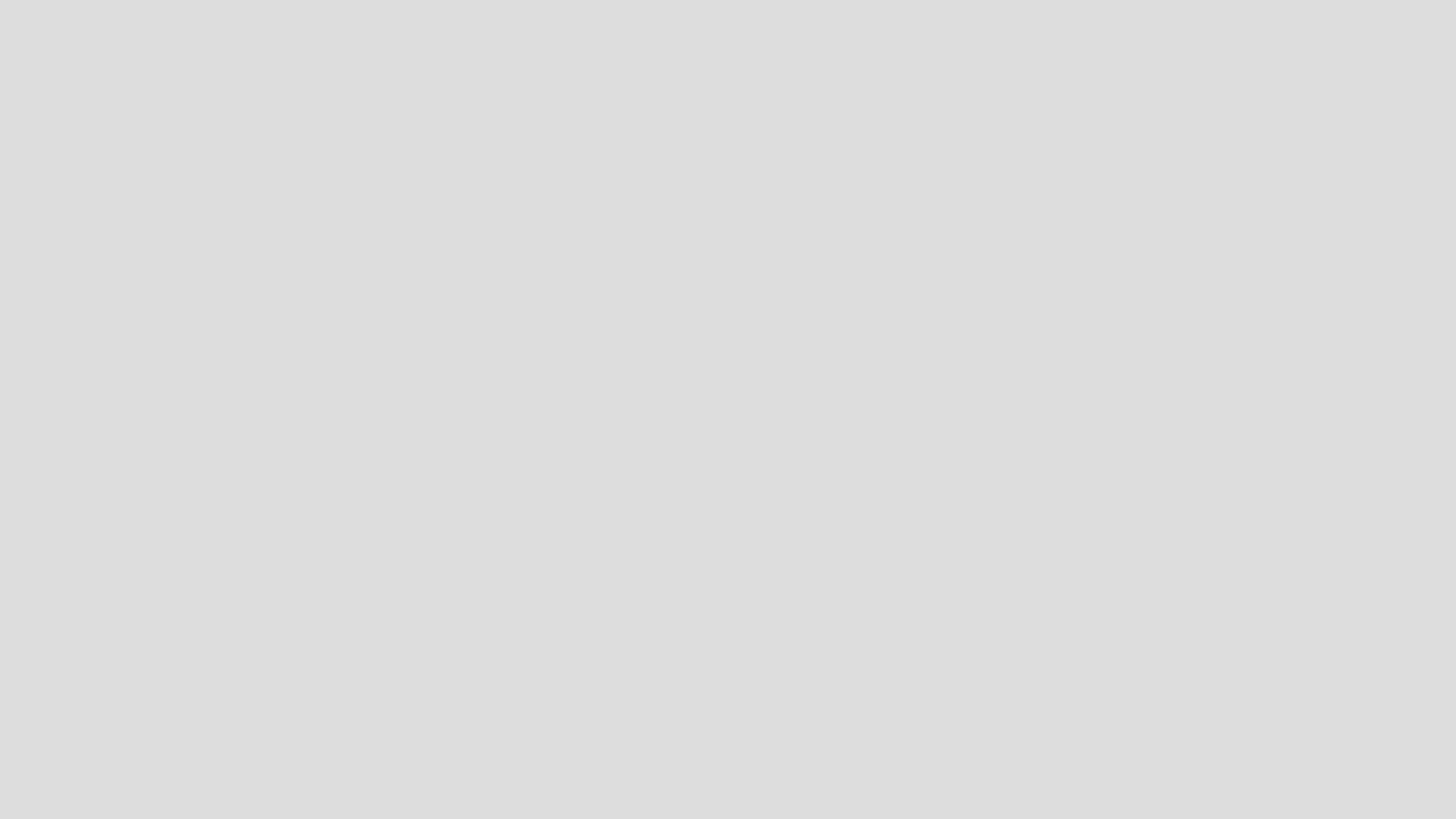

Zlínský kraj – Loukov
Čtyři identické podzemní nádrže na strategické zásoby pohonných hmot u Loukova na Kroměřížsku jsou ojedinělým technickým dílem nejen svými rozměry, konstrukčním řešením, trvanlivostí, bezpečností, ale i ekologickým přínosem. Jsou největšími podzemními nádržemi na pohonné hmoty v ČR a přitom nenarušují krajinný charakter. Kapacita každé nádrže činí 35 000 m³, což je 3,5 krát více než u běžných nadzemních nádrží. Přes všechny výhody se žádné další podobné podzemní nádrže v ČR po roce 2011 již nepostavily.
V roce 2006 se stát rozhodl posílit svou energetickou bezpečnost a požadoval doplnit sklady pohonných hmot o kapacitu 140 000 m³ motorové nafty. Nový sklad byl umístěn v Loukově v přírodním parku Hostýnské vrchy. Vlastní místo stavby se nachází na svažitém, původně zalesněném pozemku. Každá z podzemních nádrží v Loukově má kapacitu 35 000 m³, běžné ocelové, válcové, stojaté zásobníky společnosti ČEPRO, a.s. mají max. á 10 000 m³.
U nadzemních nádrží jsou také přísnější bezpečnostní, protipožární požadavky a musí být větší odstupové vzdálenosti. Umístění zásobníků pod úrovní terénu umožnilo využít zájmové území pro maximální skladovací kapacitu. S ohledem na ochranu krajiny jsou nádrže zasypány zeminou, která tvoří také zábranu proti ohni a omezuje vliv teplotních změn. Technické řešení významně zlepšuje funkci technologického zařízení.
Pro optimalizaci řešení generální zhotovitel v průběhu zakázky sestavil několik expertních skupin ze zástupců investora, projektantů a specialistů z pražského ČVUT i brněnského VUT.
Výhody podzemních nádrží pro pohonné hmoty v Loukově jsou zejména tyto:
Nádrže tvoří válcové skořepiny o vnitřním průměru 47,8 m. Výška nádrží je cca 27 m, max. hloubka náplně při plné nádrži je 20,4 m (Obr. 3 a 4). Nádrže jsou zastřešeny kupolí ve tvaru kulové skořepiny. Nádrže jsou vzájemně propojeny železobetonovou technologickou chodbou. S ohledem na ochranu krajiny jsou nádrže zasypány zeminou, která současně tvoří zábranu proti ohni, omezuje vliv teplotních změn a tak zajišťuje lepší funkci technologického zařízení.
Nádrže jsou založeny plošně na základové desce o tloušťce 600–820 mm s obvodovým věncem o tloušťce 1,2 m umístěným pod stěnami nádrže. Deska je vyspádována směrem ke středu, kde je umístěn kalník. Základová deska má tvar osmiúhelníku a je předepnuta ve dvou kolmých směrech 12 lanovými soudržnými kabely. Je uložena na kluzné spáře, aby se umožnilo její stlačení od předpětí a od smršťování betonu.
Stěny válcové nádrže mají tloušťku 600 mm, která dává konstrukci požadovanou tuhost a současně umožňuje v ní umístit betonářskou a předpínací výztuže včetně požadovaného krytí. Stěny jsou předepnuty vodorovně i svisle. Vodorovně jsou předepnuty 19 lanovými kabely, které jsou s ohledem na omezení tření situovány v plastových kanálcích. Kabely jsou vedeny v půlkruhových dráhách a jsou kotveny ve svislých žebrech. Žebra jsou po obvodě 4, kabely jsou v následujících vrstvách vzájemně pootočeny o 90 ° takže se v jednom řezu nestykuje přesahem více než 50 % kabelů. Svislé kabely jsou vedeny v dráhách tvaru U, s kotvami situovanými na horním okraji stěny. Jsou použity 12lanové kabely v ocelových kanálcích. Ve spodní části je kanálek tvořen ohnutou plnostěnnou ocelovou trubkou, aby se zajistilo spolehlivé protažení lan a aby se dodržel přesný tvar dráhy kabelů (Obr. 4 a 5). Spoj stěny a základové desky je v definitivním stavu uvažován jako pružné vetknutí, spojem neprobíhá žádná betonářská výztuž, ale je předepnut svislými kabely stěn. V době výstavby, před předepnutím stěn, byl spoj posuvný, a tak umožnil vodorovné předepnutí stěn a zmenšení průměru nádrže.
Skořepinová kupole má vzepětí 5 m a tloušťku 250 mm. Je vyztužena pouze betonářkou výztuží s výjimkou obvodového věnce, kde jsou umístěny obvodové 12lanové kabely. Střecha je propojena se stěnami pomocí přepínacích tyčí a betonářské výztuže a spoj je ztužen obvodovým předpětím.
Základová deska byla betonována z provozních důvodů ve 3 dílech (Obr. 6). Stěny byly s ohledem na eliminování pracovních spár a rychlost výstavby betonovány pomocí posuvného bednění (Obr. 7). Stěny jedné nádrže byly postaveny přibližně za 14 dní. Betonáž byla mimořádně náročná s ohledem na požadavek na pomalého tuhnutí betonu, které umožňuje navázání jednotlivých vrstev, a současně s ohledem na požadavek dostatečné pevnosti betonu umožňující posun bednění.
S ohledem na omezený prostor bylo nutno vyřešit uspořádání předpínací a betonářské výztuže tak, aby bylo možné garantovat jejich plynulé osazování a betonáže stěn. Konstrukce bednění stěn musela být také upravena tak, aby bylo možné betonovat i konzoly na horním okraji stěn, které sloužily později pro zvedání střechy a pro její ukotvení (Obr. 8).
Na základě vyhodnocení řady variant uspořádání konstrukce a technologie výstavby střechy bylo přijato řešení, ve kterém se střecha vybetonovala uvnitř nádrže na nízkém bednění situovaném na jejím dně (Obr. 9) a následně se vyzdvihla do definitivní horní polohy (Obr. 10 a 11). Významně se tak zmenšilo množství skružového materiálu a zjednodušila se jeho demontáž a transport do další nádrže.
Skořepina hmotnosti cca 1 500 tun byla vybetonována a obvodový věnec byl předepnut v dolní poloze. Zvedání pomocí závěsných tyčí o průměru 36 mm pomocí dutých válců se provádělo v krocích daných zdvihem válců cca 150 mm (Obr. 12). Při zvedání bylo nutné podrobně monitorovat geometrii skořepiny, aby nedošlo k jejímu porušení trhlinami. Při tom se musel brát v úvahu i vliv nerovnoměrného oslunění a dle naměřených deformací řídit postupné zvedání. V horní poloze byla skořepina ukotvena pomocí předpínacích tyčí a v následně dobetonovaném a předepnutém obvodovém věnci (Obr. 13).
Před instalací laminátové vystýlky byly nádrže naplněny vodou. Cílem zatěžovací zkoušky bylo ověření sedání konstrukcí a ověření jejich vodotěsnosti. Ve stěnách nebyly žádné průsaky, minimální průsaky v oblasti základové desky byly odstraněny injektáží. Po dokončení jsou celé nádrže zasypány zeminou a naplněny naftou. Nádrže, jejichž stavba proběhla podle předpokladů (Obr. 14 a 15), bezproblémově fungují.
Při realizaci bylo přemístěno zhruba 300 000 m³ zeminy, která se na stavbě znovu použila – nádrže jsou zapuštěny do dvanáctimetrové hloubky a přesypané zeminou s celoplošným vegetačním pokryvem. Ohromná hmota stavby je tak skryta pod povrchem země a souvisle navazuje na okolní krajinu. Konstrukce zásypů byly řešeny s využitím výztužných geosyntetik a zásypu z výkopku. Volná mezera tl. 300 mm mezi zásypem a stěnami nádrží zajišťuje nulové namáhání zemním tlakem od konstrukce obsypu. Výpočtem predikovaná deformace líce konstrukce obsypu dosáhla v nejkritičtějším místě po dokončení stavby hodnoty max. 18 cm. V průběhu realizace stavby docházelo a následně vlivem deformace konstrukce bude docházet k uzavírání mezery až na 12 cm.
Kolem každé nádrže se postupně realizovaly jednotlivé vrstvy (celkem jich bylo 36) – půdorysný obrys nádrží byl proveden z pásů geosyntetiky šířky 3 m, u stěny se geosyntetika pokládala s přesahem 1 m na každou stranu. Vrstvy vyztuženého zemního tělesa měly tloušťku 0,6 m, výška vyztužené konstrukce tak činí 21 m. Čelo každé vrstvy vyztužení tvoří výztužná polyesterová geotextilie s nominální pevností 600/50 kN/m, v některých částech zemní konstrukce 800/50. Odvodnění prostoru u horní části nádrží bylo zajištěno pomocí drátokamenných skluzů s fólií. Na odvodňovací skluzy je napojena hlavní hydroizolační fólie těsnění na temeni uložiště. K omezení možnosti dotace zpětných zásypů uložiště srážkovou vodou je prostor temene uložiště (mezi nádržemi) opatřen fóliovým těsněním, které je napojeno na hydroizolační systém střechy nádrží. Průsakovou srážkovou vodu odvádí tak, aby nestékala po plášti nádrží.
„V případě války, požáru či letecké katastrofy jsou podzemní nádrže mnohem bezpečnější. Údržba je spojena jen s běžnými revizemi a profylací. Stejně jako u nadzemních nádrží podléhají diagnostice každých pět let, pokud jsou detekovány náměty k opravě, zrealizují se.“
„Neobvyklý návrh 4 velkoobjemových a zároveň podzemních nádrží byl logickou nutností mimo jiné s ohledem na vliv stavby na krajinný ráz, založení nádrží a zachování vhodných odtokových poměrů po dokončení stavby. Konstrukce železobetonových nádrží se štíhlou stěnou s vnitřní dvouplášťovou výstelkou pro kontrolu těsnosti byla volena jako moderní pokročilý systém bezpečného skladování pohonných hmot. Velkou výhodou je kompaktní konstrukce, která umožnila splnění požadavku umístit na omezenou plochu potřebnou kapacitu. Umístění bylo optimalizováno tak, aby i při velmi velkých objemech zemních prací byla jejich bilance vyrovnaná a nevznikl tak významný požadavek na zajištění náhradních materiálů ani na odstranění přebytků výkopového materiálu. Konstrukční řešení nadrží bez vnitřních podpor pak umožňuje jednoduchou a zároveň účinnou homogenizaci uložených pohonných hmot ejektorem na produktovém potrubí v nádrži. Uspořádaní nadrží a jejich vystrojení umožňuje dle potřeby mimo jiné výhodné gravitační vypouštění jednotlivých nadrží do navazujících produktových rozvodů.“
„Klasické ocelové nadzemní nádrže vyžadují protikorozní úpravu, kterou je nutné pravidelně obnovovat. Inovace spočívala především v návrhu betonových předpjatých nádrží s laminátovou vystýlkou, která má delší trvanlivost. Plánovaná životnost betonových nádrží by měla být cca 2x delší než u podobných ocelových. Vnitřní dvouplášťová výstelka byla v takto velkých nádržích provedena poprvé v ČR. Kromě toho, že zabrání úniku produktu z nádrží, dokáže pomocí podtlakového systému identifikovat i jejich případnou netěsnost. Jejich umístění pod zem je jen dalším bonusem.“
„Začali jsme už v únoru 2007 s inženýrskou, předprojektovou a projektovou přípravou. To, že jsem mohl stavbu sledovat od začátku, pro mě bylo důležité. První etapu jsme zakončili zhutněním roznášecích podkladních vrstev pod nádržemi, druhá zahrnula samotnou realizaci čtyř tenkostěnných nádrží. Pomocí taženého bednění rostly do výšky v průměru o 1,4 metru denně. Betonové válce s průměrem téměř 48 m a výškou 27 m vyplnily jako čtyřlístek téměř celé staveniště. Při zátěžových zkouškách jsme si pak ověřili, že jejich pokles se i přes nehomogenní podloží pohybuje jen v rozmezí návrhových hodnot.“
„Po dokončení byly nádrže zasypány zeminou o objemu více než 300 000 m³. Bylo nutné přesně propočítat a najít takový způsob, aby nedošlo k jejich porušení nerovnoměrnými tlaky. To se povedlo. Zasypané nádrže jsou plně funkční a téměř neviditelné.“