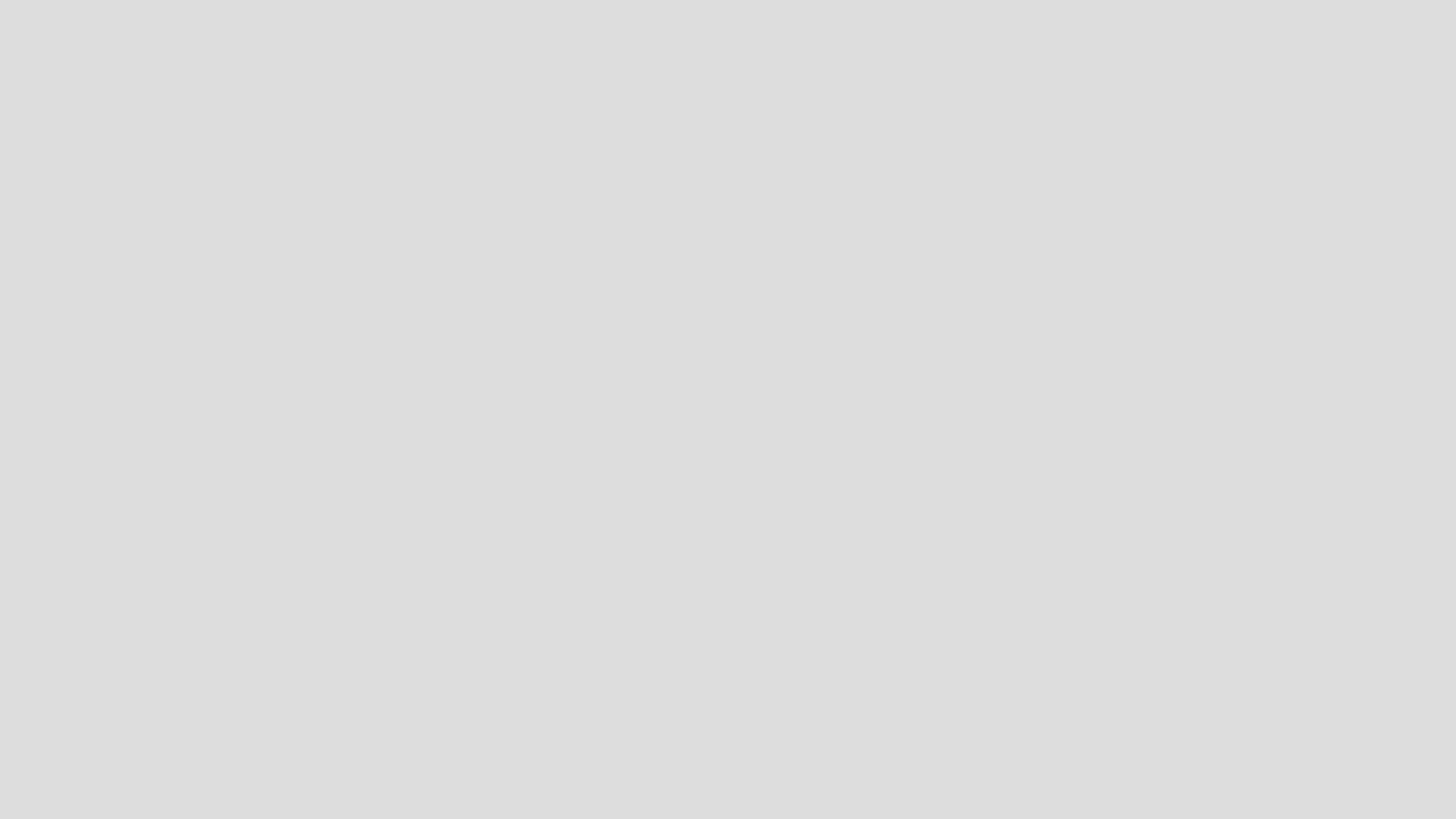

Hlavní město Praha – Trasa metra IV C1, Holešovice–Troja
Výstavba trasy pražského metra C mezi stanicemi Holešovice a Kobylisy probíhala zcela unikátním způsobem. Směrově a výškově zakřivené tubusy se vybetonovaly na břehu v suchém doku a potom vysunuly po betonové dráze do rýhy vyhloubené na dně řeky. Klasické zaplavování tunelů nebylo možné, proto bylo nutné použít originální metodu výstavby s mnoha dílčími, dosud neodzkoušenými technologiemi. Volba alternativní technologie se však hlavnímu městu více než vyplatila nejen v podobě nižších nákladů a rychlejší výstavby, ale i omezením škod, které mohla na stavbě způsobit ničivá povodeň v roce 2002.
Stanice metra Nádraží Holešovice byla postavena dříve, než bylo vyřešeno, zda trasa C křižující Vltavu povede mostem nebo tunelem. Poté byl schválen projekt, podle nějž metro mělo vést tunelem umístěným těsně pode dnem řeky a stavba měla být prováděna v otevřené stavební jámě. Dodavatel stavby Metrostav a.s. předložil při výběrovém řízení i alternativní variantu vysouvaných tunelů, jejíž výhodou bylo zejména urychlení výstavby a snížení nákladů. Investor ji proto vybral k realizaci.
Protože tunelové trouby jsou zakřivené v půdorysu i výškově a nebylo možné použít klasické zaplavování, navrhli stavební inženýři originální metodu pod vodou vysouvaných tunelů. V rámci tohoto řešení tunelové trouby neplavaly, ale svým zadním koncem se posouvaly po betonové dráze na definitivní místo v rýze vykopané ve dně řeky.
Požadovaný tvar tunelových tubusů se vybetonoval ve stavební jámě na trojském břehu Vltavy. Vzhledem k tomu, že šlo o unikátní technologii výstavby, která zahrnovala řadu dílčích problémů, vytvořil zhotovitel technickou radu. Zastoupeni v ní byli nejen jeho odborníci, ale i autoři původní projektové dokumentace, experti z ČVUT i ze zahraničí.
Hlavní výhodou byla rychlost výstavby. Doba výstavby tunelů pod řekou se zkrátila ze 3 let prakticky na 2 roky. Kromě toho se kritická cesta přesunula do jiných úseků trasy. Tunely byly betonovány v suchém doku, tedy v relativně příznivém prostředí za sucha, kdy bylo možné zajistit vysokou kvalitu jejich provedení. Použití vodonepropustného betonu a příslušných detailů zajišťujících vodotěsnost tunelů přispělo k jejich vysoké kvalitě a odbourání nákladů a problémů s hydroizolací, která zcela odpadla. Obrázky ukazují částečně zaplavené tubusy a výstavbu definitivních tunelů v suchém doku.
Výkopové práce byly omezeny na minimum nutné k umístění tunelů do definitivní polohy v řece. Suchý dok byl vytěžen v místě budoucích pokračování tunelů, tj. nepředstavoval žádný výkop navíc.
Výkopy v řece byly minimalizovány na rýhu pro tunely. Minimální výkopy a zásahy do břehových částí jsou pozitivně hodnoceny též z ekologického hlediska a vzhledem k vlivu výstavby na životní prostředí.
Stavební činnost prováděná v korytě řeky také minimálně narušila lodní provoz. Výkopové práce se prováděly z lodí a k zastavení lodního provozu došlo pouze v době výsuvu 2. tubusu na cca 1 týden. Výsuv 1. tubusu byl naplánován do plavební přestávky, která má jiné důvody a opakuje se každý rok.
Riziková doba ohrožení byla oproti klasické výstavbě v jímkách minimální. Tato skutečnost se neplánovaně ověřila při povodních v srpnu 2002. Celkové náklady na výstavbu tunelů pod řekou byly nižší než u klasického postupu. Přitom se ověřila aplikace vodotěsného betonu na tunely metra a získala se řada poznatků aplikovatelných pro další stavby.
Výstavba pro obě tunelové trouby probíhala dvakrát téměř identicky. Celý tunel byl vybetonován ve stavební jámě (suchém doku) na pravém (trojském) břehu řeky. Současně se ve dně vytěžila rýha, protože tunely jsou zcela skryty ve dně řeky. Po technologickém vystrojení tunelu se suchý dok zaplavil a otevřela se štětová stěna oddělující dok od řeky. Tunel se v přední části zavěsil na ponton a zadní část spočívala na hydraulických teleskopických kluzných nohách. Pak následoval „výsuv“, tj. přesun tunelu ze suchého doku do rýhy v řece. K tomu sloužilo hydraulické tažné a brzdné zařízení. Po vysunutí prvního tunelu se dok opět vysušil, vybetonoval se v něm druhý tunel a ten se stejným způsobem vysunul opět do řeky. Obr. 1 ukazuje tunely v betonážní poloze a v definitivní poloze v řece. Obr. 2 pak znázorňuje suchý dok včetně vybetonovaného prvního tubusu před jeho zatopením. Po dalším vysušení doku se v něm vybetonovaly definitivní tunely připojující vysouvané části pod Vltavou k pokračujícím tunelům směrem k ražené části ve svahu do Kobylis. Jedna stavební jáma byla využita celkem třikrát, výkopy byly minimalizovány na nejnutnější rozsah.
Výstavba začala těžbou stavební jámy – suchého doku – koncem roku 2000. Suchý dok byl ohraničen kotvenými milánskými stěnami. Suchý dok byl oddělen od řeky jednoduchou ocelovou štětovou stěnou. Ta byla vysunuta do řeky cca 12 m. Tak vznikla malá jímka u trojského břehu. Podobně byla vytvořena i menší jímka na holešovickém břehu.
Výkopy v řece znamenaly vytěžit cca 60 000 m³ ze dna Vltavy. Dno je složeno z vrstvy štěrkopísků o mocnosti cca 4–5 m. Pod nimi se nachází vrstva jílovitých břidlic. Během těžby se používaly drapáky různých konstrukcí a odstřel nebyl nutný. Nejprve se těžila svahovaná rýha pro tunel pravé koleje. Rýha byla hloubena tak, aby mezera mezi dnem tunelu a dnem rýhy byla v rozmezí 300–500 mm.
V suchém doku se připravovaly pomocné konstrukce pro betonáž a následné práce. Základem byla výstavba betonových podélných prahů. Tyto v principu základové pásy měly tři funkce: 1. Sloužily jako základ pro výstavbu tunelu v poloze „betonáž“. 2. Poskytovaly základ pro připevnění kolejnic, po kterých se pohybovalo posuvné bednění – forma – pro betonáž tunelu. 3. Tvořily kluznou dráhu pro přesun tunelu do definitivní polohy. Tyto podélné prahy byly umístěny pod stěnami budoucího tunelu. Mezi nimi byl prostor vyplněn štěrkem, aby se vytvořil vodopropustný podklad pro zajištění vztlaku působícího na tunel.
Betonáž patřila v rámci projektu k nejnáročnějším činnostem. Konstrukční beton tubusu zajišťoval kromě nosné funkce též vodotěsnost celé konstrukce. Tunely nemají žádnou další izolaci proti vodě, a proto se v konstrukci nesměly vyskytovat žádné trhliny. Průřez tubusu má vnější rozměry 6,48 × 6,48 m, tloušťky horní a spodní desky 700 mm a tloušťky stěn 730 mm. Délka tubusu činila 168 m. Pro betonáž byl tubus rozdělen na 14 segmentů o délce 12 m.
Pro betonáž tunelů byl zvolen způsob betonáže segmentů v jednom pracovním záběru. Důvodem bylo menší riziko vzniku trhlin od teplotních gradientů. Přestože se vyloučily podélné pracovní spáry, zůstávala stále svislá pracovní spára mezi jednotlivými segmenty, která byla těsněna několika způsoby.
Dalším problémem při betonáži bylo přesné dodržování tvaru a rozměrů konstrukce. Nadměrné odchylky od projektovaného tvaru by byly příčinou příliš těžkého nebo naopak příliš lehkého tubusu. Tíha tubusu včetně ocelových doplňků je asi 6 700 t. Tíha tubusů ve vodě byla u prvního tunelu 70 t a u druhého 57 t, což je přibližně 1 %. Zbývajících 99 % tíhy tvoří nadlehčující síla rovná tíze objemu vytlačené vody. Z toho plyne velká citlivost výsledné tíhy tubusu ve vodě na jakékoli odchylky v rozměrech nebo v objemové tíze betonu a dalších parametrech.
Aby se omezily tolerance v rozměrech, byla forma pro betonáž tubusu velmi tuhá. Její konstrukce, navržená pro účely projektu ve spolupráci s firmou PERI (Obr. 3). Vysoká tuhost všech konstrukčních dílů zajistila odchylky v tloušťkách menší než 10 mm, v průměru pouze asi 3 mm.
Zakřivený tubus (Obr. 4) je ve vodě nestabilní, což bylo jedním z důvodů, proč klasické zaplavování v našem případě nebylo použitelné. Přistoupilo se k manipulaci, kdy tubus byl v přední části zavěšen na pontonu a v zadní části spočíval na dráze na kluzných teleskopických nohách. Již návrh rozměrů předpokládal, že pokud budou dodrženy předepsané tolerance, je vyvážení reálné. Existuje však statistická variabilita jednotlivých parametrů (rozměry průřezu, odchylky objemové tíhy betonu, nepřesnosti měření atd.), s níž je nutné počítat a kterou nelze odhadnout předem. Proto byl tubus vybaven třemi skupinami nádrží na vodu, pomocí kterých bylo možné tunel přitížit či odlehčit. Po jeho teoretickém vyvážení byl tunel zvážen pomocí hydraulických válců umístěných pod tubusem.
Na tubusu byla připevněna řada prvků. Patřily k nim ocelové teleskopické nohy, vodicí nosník deviátoru, kotevní prvek brzdného závěsu, kotvení pontonu a plechy pro následné těsnění koncových jímek, ocelová víka tunelu o hmotnosti cca 8,5 t a vyvažovací nádrže.
Hydraulické válce umístěné pod tubusem a na zadních teleskopických nohách (Obr. 5) sloužily k vážení tubusu a zadní pak k jeho nadzvednutí pro manipulaci. Válce byly v činnosti po zaplavení doku, takže k nim již nebyl běžný přístup. Aby bylo možné kontrolovat výšku zdvihu pístu na válcích, byly vybaveny zařízením k měření zdvihu.
Ponton o rozměrech 6 × 9 m měl nosnost kolem 50 t (Obr. 6). Reálně využitá kapacita byla v případě 1 tubusu 15 t, v případě 2 tubusu 19 t. Ponton byl vybaven dvojicí hydraulicky rektifikovatelných svislých závěsů, které nesly tubus prostřednictvím příčníku přivařeného ke kotevním plechům na stropě tubusu.
Během výsuvu na tubus působily různé síly ovlivňující jeho namáhání a stabilitu. V přední části tubusu působily tažné síly ve dvou směrech vymezených polohou tubusu a polohou tažných jednotek na protějším břehu Vltavy. Na zadním konci tubusu působily též dvě síly, a to brzdná síla vyvolaná odporem odvíjeného brzdného závěsu a příčná síla bočního vedení na výsuvné dráze, která se přenášela do tubusu přes kluznou ližinu. Další vodorovné zatížení tubusu představoval tlak proudu a tření na kluzných ližinách. Změna směru tažné síly vyvolaná buď rozdílnou rychlostí tahu na tažných jednotkách, nebo účinkem příčného zatížení proudem okamžitě způsobila změnu směru pohybu čela tubusu. Zadní konec tubusu se pohyboval pouze po dráze, proto nebylo nutné jej směrově ani výškově řídit. Tažné závěsy byly zpočátku upevněny na předním konci tubusu. Tím bylo zajištěno, že závěsy spolehlivě projdou otvorem ve štětové stěně a dále, že jejich úhel bude co největší. Čím je větší úhel rozevření tažných závěsů, tím je i citlivost řízení směru pohybu větší (to platí do rozevření cca 90°). Během posunu se úhel stále rozevíral a pokud by se v pohybu takto pokračovalo až do konce, dosáhl by až téměř 180°. To by nebylo možné, protože by se zcela vytratila složka síly táhnoucí tunel dopředu. Proto bylo nutné přibližně v polovině dráhy přesunout tažný bod na tubusu směrem dozadu o cca 45 m. Tím došlo k opětnému sevření úhlu závěsů, avšak bylo možné dotáhnout tubus až do konečné polohy, kde úhel závěsů svíral právě přibližně 90°. To znamená, že až do konce pohybu byly síly vyvolané tažnými jednotkami efektivně využívány. K přesunu tažného bodu na tubusu sloužil tzv. deviátor.
Deviátor (Obr. 7) lze přirovnat k jezdci pohybujícímu se po vodicím nosníku. Tažná lana vedla od tažných jednotek k deviátoru a dále podél vodicího nosníku k jeho zadnímu konci, kde byla ukotvena. Pokud byl deviátor na předním konci tubusu, tažné síly v lanech se přenášely na čelo tubusu přes vodicí nosník. Přesunem deviátoru po nosníku se lana uvolnila z čela tubusu a tažné síly se přenášely prostřednictvím deviátoru na tubus v místě, kde se právě deviátor nacházel. Tím bylo dosaženo změny polohy tažného bodu.
Tažné jednotky sestávaly z dvojice přímočarých hydraulických válců umístěných v ocelovém rámu (Obr. 8). Rám se otáčel kolem čepu připevněného k základu, aby se umožnilo natáčení směru tažné síly podle polohy tubusu během výsuvu. Tažná síla byla vyvolána jedním z válců, který byl aktivní. Druhý z válců se zatím vracel do počáteční polohy.
Brzdná jednotka sestávala z velkého brzdného válce a brzdného bubnu. Brzdný válec sloužil k zajištění polohy tubusu v době, kdy nebyl v pohybu, k zabrzdění pohybu a k případnému pohybu tubusu směrem zpět. To však nebylo ani v jednom případě nutné. Brzdný buben (Obr. 9) byl ovládán dvěma hydromotory s převodovkami a vytvářel odpor proti uvolňování brzdného závěsu navinutého na bubnu. Tím vznikala provozní brzdná síla, jejíž hlavní cíl spočíval v předepnutí tažných závěsů. Tím též došlo ke zvětšení tažných sil a ke zvýšení přesnosti řízení pohybu.
Před zahájením výsuvu tubusu bylo třeba splnit řadu podmínek. Tubus musel být pečlivě vyvážen a vystrojen kompletním zařízením. Rýha v řece musela být dokončena a zkontrolována s ohledem na nepředvídané překážky výsuvu. Průtok v řece neměl s ohledem na možné síly vyvolané proudem přesahovat 80 m³/s. Hladina byla sledována na jezu, aby nedošlo k jejímu kolísání, zvláště v době od usazení tubusu do odstranění pontonu.
Výsuv byl zahájen aktivací tažných jednotek a uvolněním brzdného závěsu na hlavním brzdném válci. Směr byl řízen ovládáním rychlostí na jednotlivých tažných jednotkách. Informaci o poloze tubusu ve vodě poskytoval navigační systém prostřednictvím údaje o podélné souřadnici posunu a o směrové odchylce od projektované trasy pohybu. Přibližně v polovině dráhy se rychlost snížila a deviátor se postupně přesunul do zadní polohy. Pak se opět rychlost zvýšila a pokračovalo se až k protějšímu břehu. Bezprostředně před dosažením koncové polohy se přesně upravila výška, tubus se pomalu dosunul na místo a položil na předem vybetonovaný práh v holešovické jímce. Doba trvání výsuvu byla v případě prvního tubusu 9 hodin a případě druhého tubusu jen 7,5 hodiny. Schéma výsuvu je naznačeno na obr. 10. Obr. 11 ukazuje přední stožár vysouvaného tubusu během pohybu, v pozadí je vidět ponton projíždějící otvorem ve štětové stěně.
Poté se zajistila poloha čela tubusu rozepřením v holešovické jímce. Následovalo spuštění zadní části tubusu na příčný práh v trojské jímce pomocí hydraulických válců na zadních teleskopických nohách.
Po dočasném usazení přistoupilo Zakládání staveb, a. s. k definitivnímu podepření a zakotvení tubusů. První tubus byl podepírán soustavou textilních vaků vyplněných betonem. Dno rýhy tvořené břidlicemi je homogenní a relativně tuhé. Do mezery mezi tubus a dno rýhy o tloušťce 300–500 mm potápěči vložili textilní vaky. Vaky byly pak pomocí svislých trub vyplněny betonem. Dvojice vaků umístěných v příčném směru pod stěnami tubusu byly od sebe v podélném směru vzdáleny 6 m.
Pro druhý tubus byla navržena jiná varianta definitivního podepření. Pod tubus bylo vloženo pouze 6 dlouhých vaků ve tvaru příčníků. Tyto dlouhé vaky byly umístěny na předem vybetonované příčné pásy podkladních betonů. Podkladní betony se vybetonovaly dříve, než se vysouval tubus. Po vyplnění vaků betonem následoval zásyp tubusu. Mezi příčníky vznikl dutý prostor, který byl pak proinjektován jílostruzkovou suspenzí. Výhoda tohoto podepření spočívala především ve zjednodušení a urychlení prací.
Každý z tubusů o délce 168 m tvoří jeden dilatační díl. Na konci tubusů byla navržena dilatační spára, též s trojnásobným jištěním proti průsaku vody, jež odděluje přilehlé části břehových tunelů, které jsou rovněž zhotoveny z vodotěsného betonu.
„Projekt vysouvaných tunelů skončil jejich úspěšným dokončením i za podmínek ovlivněných povodní v srpnu 2002. Navržená technologie se osvědčila po všech stránkách. Způsob řízení projektu od vedení firmy až po posledního dělníka na stavbě se ukázal jako vhodný a lze jej doporučit i pro další stavby. Veřejná soutěž pro výběr dodavatele splnila plně svůj účel, když vyústila v návrh lepší technologie výstavby, než předpokládal tendrový projekt. Každá soutěž by měla připouštět variantní řešení, i když to může být příčinou jejího obtížnějšího vyhodnocení.“
„My jsme tehdy ve výběrovém řízení nabídli realizaci stavby dle zadávací dokumentace, ale zároveň můj tým navrhl alternativní řešení, které by bylo bezpečnější, rychlejší i levnější. S nápadem zapustit tunel přišli jako první naši inženýři Jaromír Šob a Zdeněk Tobolka. Mojí pravou rukou při zpracování alternativního řešení byl Honza Vítek. Do týmu jsme přizvali i kolegy z Dánska, Holandska, Švýcarska. Druhý tubus jsme vysunuli na jeho pozici těsně před povodněmi. Tisíciletá voda, která před dvaceti lety zaplavila Prahu, však tunelu téměř neuškodila. Tubus se posunul jen o 30 cm, což jsme snadno napravili. Kdybychom akceptovali původní řešení, byla by stavba dražší, trvala by déle a povodně by ji ještě o několik let prodloužily. Bohužel dnes investoři jen zřídka připouští variantní řešení, i když jim to zákon o zadávání veřejných zakázek umožňuje. Chybí nejen odvaha investora, ale i kvalifikovaná výběrová komise, která by uměla alternativní nabídky posoudit. Pokud je nabídková cena hlavním kritériem, je rozhodování mnohem jednodušší. Pro investora to však z dlouhodobého hlediska není výhodné, neboť nezíská technicky krásné, časově i ekonomicky lepší řešení.“